In-house tool design
GrisGroup is a member of, and an expert in, standards bodies (UNM AFNOR-ISO) and research bodies (CETIM), as well as the German fastener trade association (DSV) and the German flat steel fabricators’ association (IBU).
Our expertise lies in the collaboration of dozens of mechanical engineers and technicians from our R&D, design and manufacturing departments. This collaboration ensures constant quality and optimisation of tooling to guarantee maximum service life.
Our resources:
adapted and modern tools
The design office is equipped with CAD workstations to design and manufacture tools dedicated to the specific problems of each customer.
Software: Solidworks, COLDFORM®, Logopress
Machining processes: turning, milling, electro-erosion, grinding
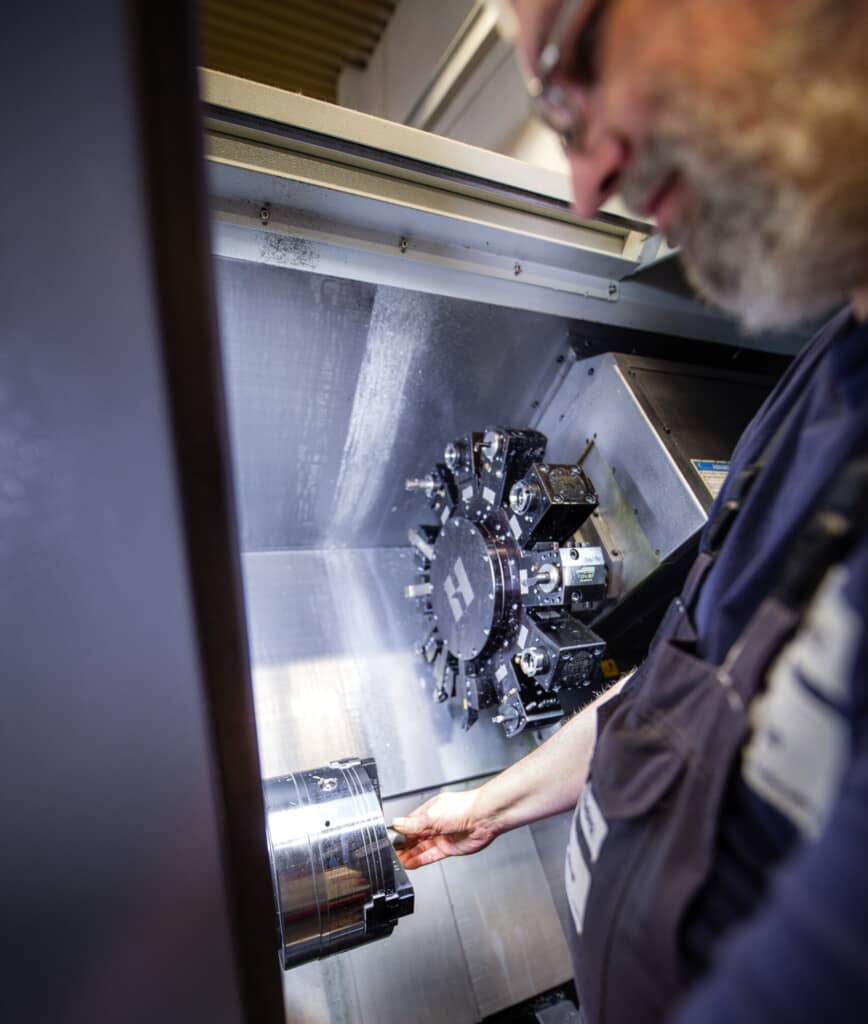